Introduction: Why PE Film Recycling Matters
The global drive toward sustainability is fueling rapid growth in the plastics recycling industry. For investors and recycling professionals, polyethylene (PE) film is a critical and complex segment—not limited merely to grocery bags. PE films vary significantly in composition, strength, and, crucially, cleaning requirements. Recognizing and understanding these variations are essential for optimizing recycling processes, reducing operational costs, increasing material recovery, and enhancing profitability.
This comprehensive guide explores the main types of PE film, their unique washing challenges, and opportunities for investment in this rapidly evolving market.
Understanding the PE Film Family: LDPE, LLDPE, and HDPE
Although grouped under the polyethylene category, variations in molecular structure result in distinct properties and recycling challenges:
1. Low-Density Polyethylene (LDPE)
- Characteristics: Flexible, transparent, low tensile strength, excellent moisture barrier.
- Common Uses: Plastic bags, shrink wraps, agricultural films, food packaging.
- Recycling Challenges: Susceptible to tearing and tangling in machinery; frequent contamination by food residues, labels, and inks.
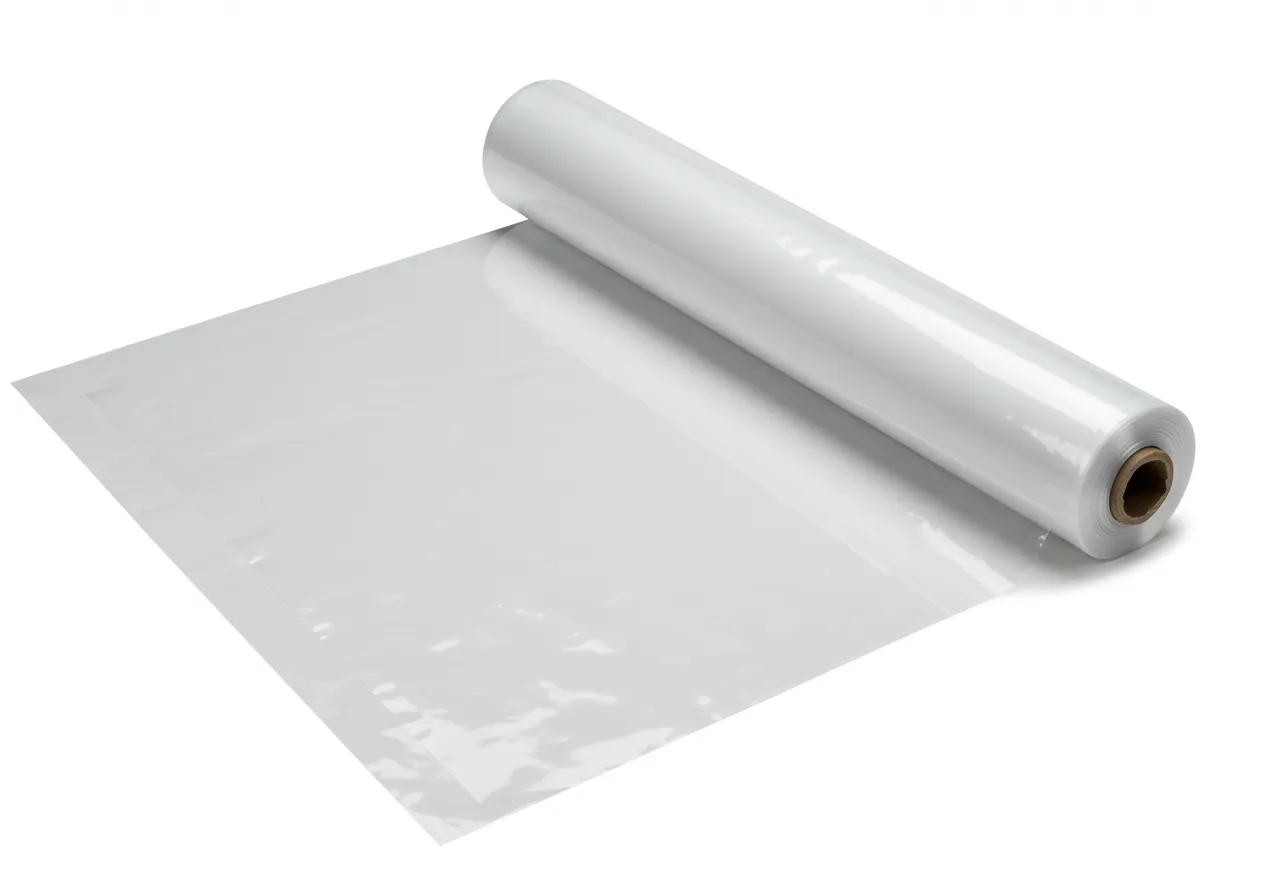
2. Linear Low-Density Polyethylene (LLDPE)
- Characteristics: Higher tensile strength and puncture resistance than LDPE; exceptional stretchability.
- Common Uses: Pallet wraps, industrial liners, geomembranes, certain food packaging films.
- Recycling Challenges: Still prone to tangling; adhesive residues from tapes and labels; often contaminated with warehouse debris and dirt.
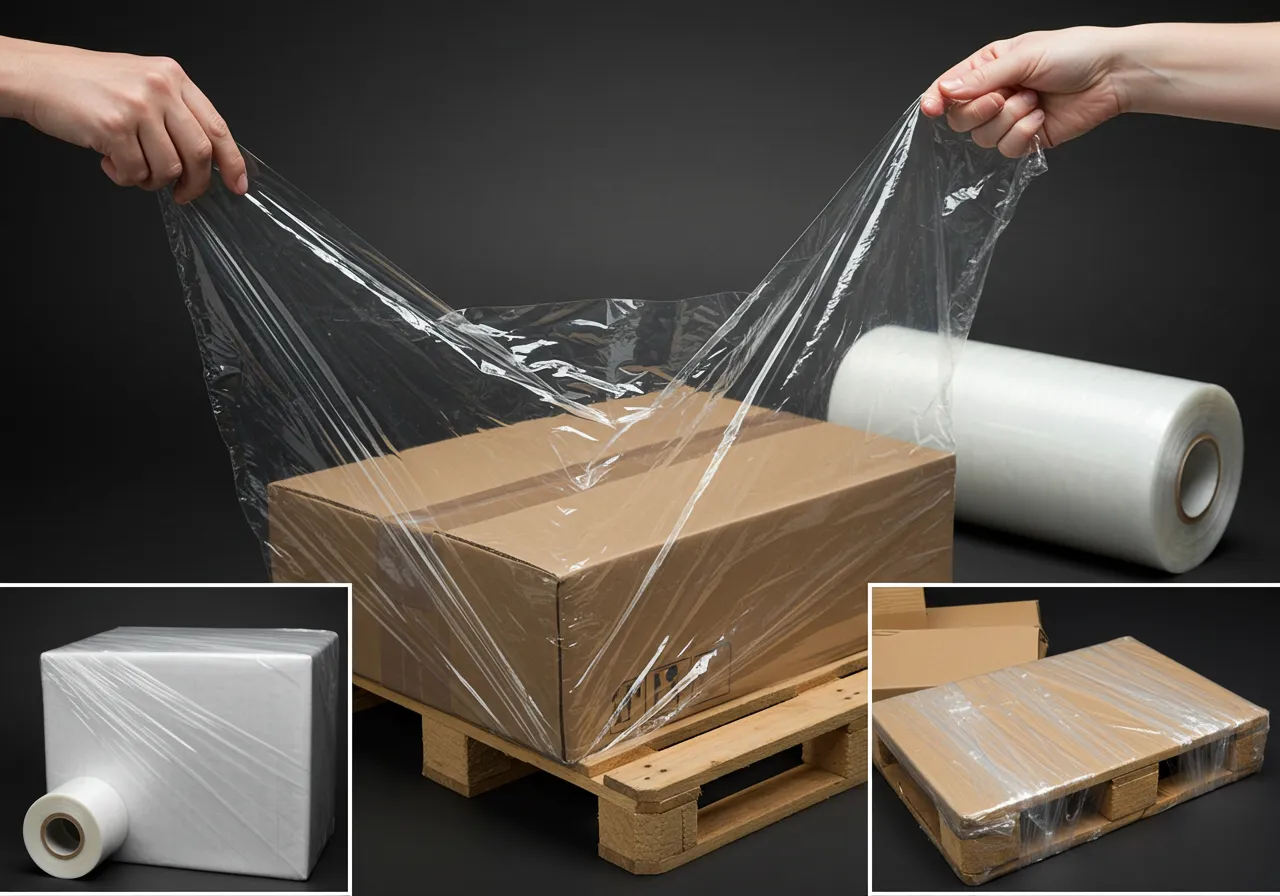
3. High-Density Polyethylene (HDPE)
- Characteristics: Stronger and stiffer than LDPE/LLDPE; higher chemical resistance; less transparent.
- Common Uses: Thicker grocery bags, mulch and agricultural films, industrial and construction films.
- Recycling Challenges: Less prone to tangling but frequently heavily soiled with mud, pesticides, and inks, especially in agricultural applications.
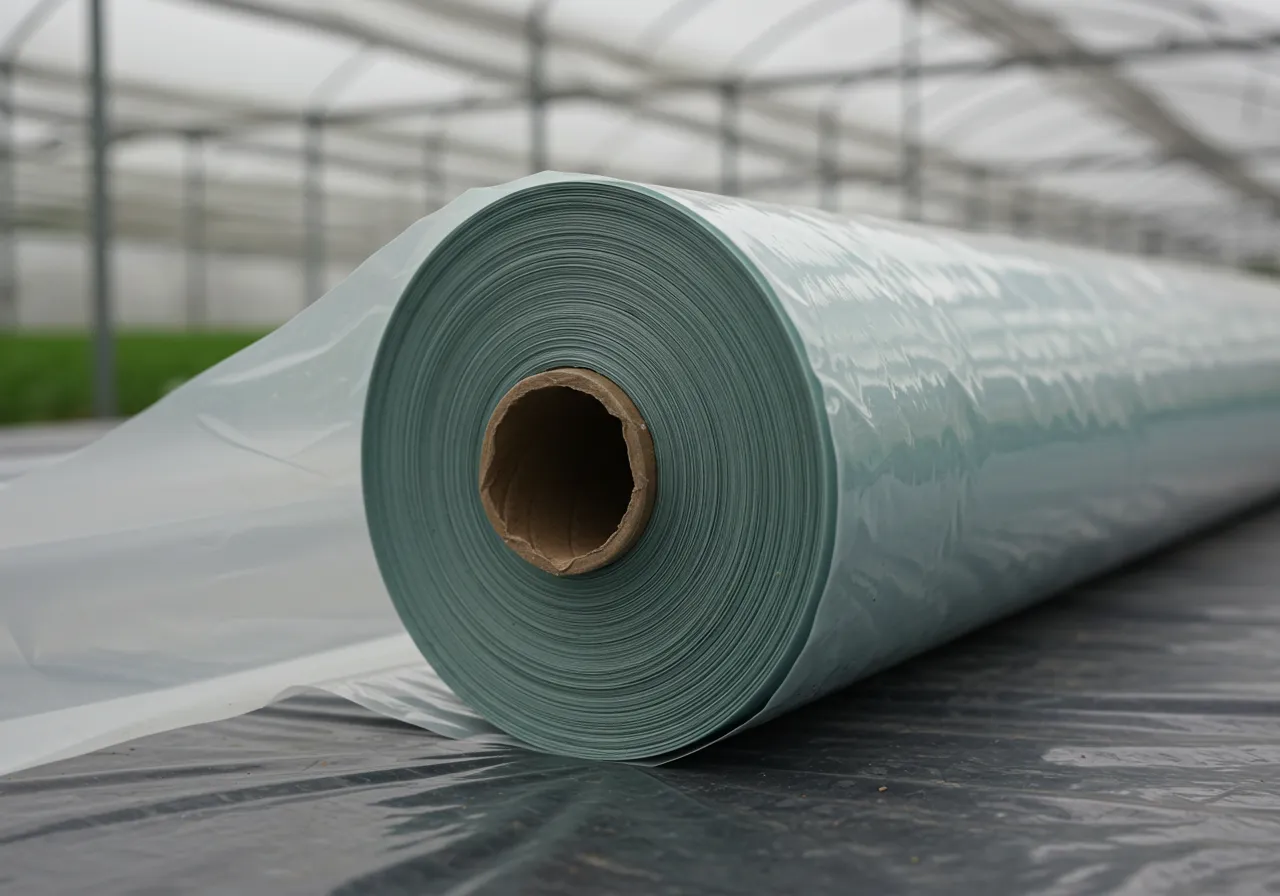
The PE Film Washing Process: Customized Solutions for Better Results
Effective washing is essential for removing contaminants and ensuring high-quality recycled PE film. The cleaning process must be adapted according to film type and contamination level:
1. Pre-Sorting & Shredding
- Removing non-PE materials (metals, paper, cardboard).
- Shredding to simplify handling and washing.
2. Trommel Screen & Pre-Wash
- Rotating drums screen out loose dirt and debris.
- Initial washing loosens stubborn contaminants.
3. Friction Washing (Critical Step)
- Rotating paddles or screws scrub contaminants from film surfaces.
- Controlled use of water, heat, and detergents tailored to film type:
- LDPE & LLDPE: Sensitive to temperature and detergent concentration.
- HDPE: Can withstand more aggressive cleaning.
4. Sink-Float Separation
- Exploits density differences; PE floats, heavy contaminants (PVC, sand, grit) sink.
- Essential for ensuring recyclate purity.
5. Rinsing & Dewatering
- Multiple rinse cycles eliminate residual detergents and contaminants.
- Centrifuges or screw presses remove excess water.
6. Drying
- Hot air drying prepares clean film flakes for extrusion and pelletizing.
7. Optional Optical Sorting
- Advanced sorting systems remove residual contaminants by color or material type, further increasing purity.
Overcoming Specific Contamination Challenges
Addressing unique contaminants requires specialized solutions:
- Adhesives (Labels, Tapes):
Hot-water washing, enzymatic treatments, and specialized detergents. - Inks:
Chemical-based de-inking treatments prevent discoloration and maintain recyclate quality. - Food Residue (LDPE):
Intensive washing with hot water and detergents to eliminate biodegradable residues and odors. - Agricultural Contaminants (HDPE):
Pre-washing and aggressive friction washing remove heavy dirt and pesticide residues. - Mixed Plastics (PET, PVC):
Careful sorting and advanced separation techniques to avoid contamination during recycling.
Investment Opportunities and Market Growth Trends
The PE film recycling market is rapidly expanding, driven by:
- Growing Consumer Demand for Sustainability:
Brands are increasingly expected to incorporate recycled content. - Government Regulations & EPR Schemes:
Policies incentivize recycling and place responsibility on manufacturers and producers. - Technological Innovations:
Improved washing and sorting technologies boost recyclate quality and process efficiency. - Circular Economy Initiatives:
A shift toward circular practices propels market opportunities.
Investment possibilities span the entire PE film recycling value chain:
- Collection & Sorting Infrastructure:
Enhancing post-consumer film recovery systems. - Advanced Washing & Processing Facilities:
State-of-the-art facilities tailored to diverse film types and contamination challenges. - High-Quality Recyclate Production:
Manufacturing premium recycled PE pellets for industrial reuse. - R&D in Recycling Technologies:
Innovating in washing, de-inking, and contaminant removal techniques. - Emerging Chemical Recycling:
Although still developing, chemical recycling represents significant potential.
Conclusion: The Bright Future of PE Film Recycling
PE film recycling is a complex yet crucial component of global sustainability efforts. Mastering the nuances between PE film types and addressing their specific washing and processing requirements will enhance recycling efficiency and profitability. Success in this market will rely on continued technological innovation, collaboration along the supply chain, and adaptation to evolving regulations.
The future of PE film recycling is not only promising—it’s essential.
Ready to Invest in PE Film Recycling?
Contact us today to discover how we can guide you through investment opportunities and help you thrive in the dynamic polyethylene recycling industry.