Introducing the innovative PET Bottle Recycling Machine, designed to streamline the recycling of polyethylene terephthalate (PET) bottles. This advanced machine efficiently crushes, shreds, and sorts PET bottles, transforming waste into valuable recycled material. With cutting-edge technology at its core, it not only reduces environmental impact but also boosts productivity in recycling facilities.
Equipped with user-friendly interfaces, energy-efficient features, and low maintenance costs, our PET Bottle Recycling Machine helps businesses reduce operational expenses while contributing to a more sustainable future. Ideal for plastic manufacturers, recycling plants, and environmental initiatives, this machine offers an effective solution for waste management and resource recovery.
Take the next step toward a cleaner, more efficient recycling process with our PET Bottle Recycling Machine.
Key Features
Key Components

Debaler Machine
The first step in our plastic bottle washing line is to break the compacted bales of PET bottles into a free-flowing stream. Once the bales are “busted”, the bottles can move freely onto the next machine.
Trommel
An optional piece of equipment, the trommel is a slowly rotating tunnel lined with small holes that are slightly smaller than the PET bottles. Small pieces of contamination such as glass, metals, rocks/dirt, paper, etc. can fall through the holes while the PET bottles move onto the next machine.
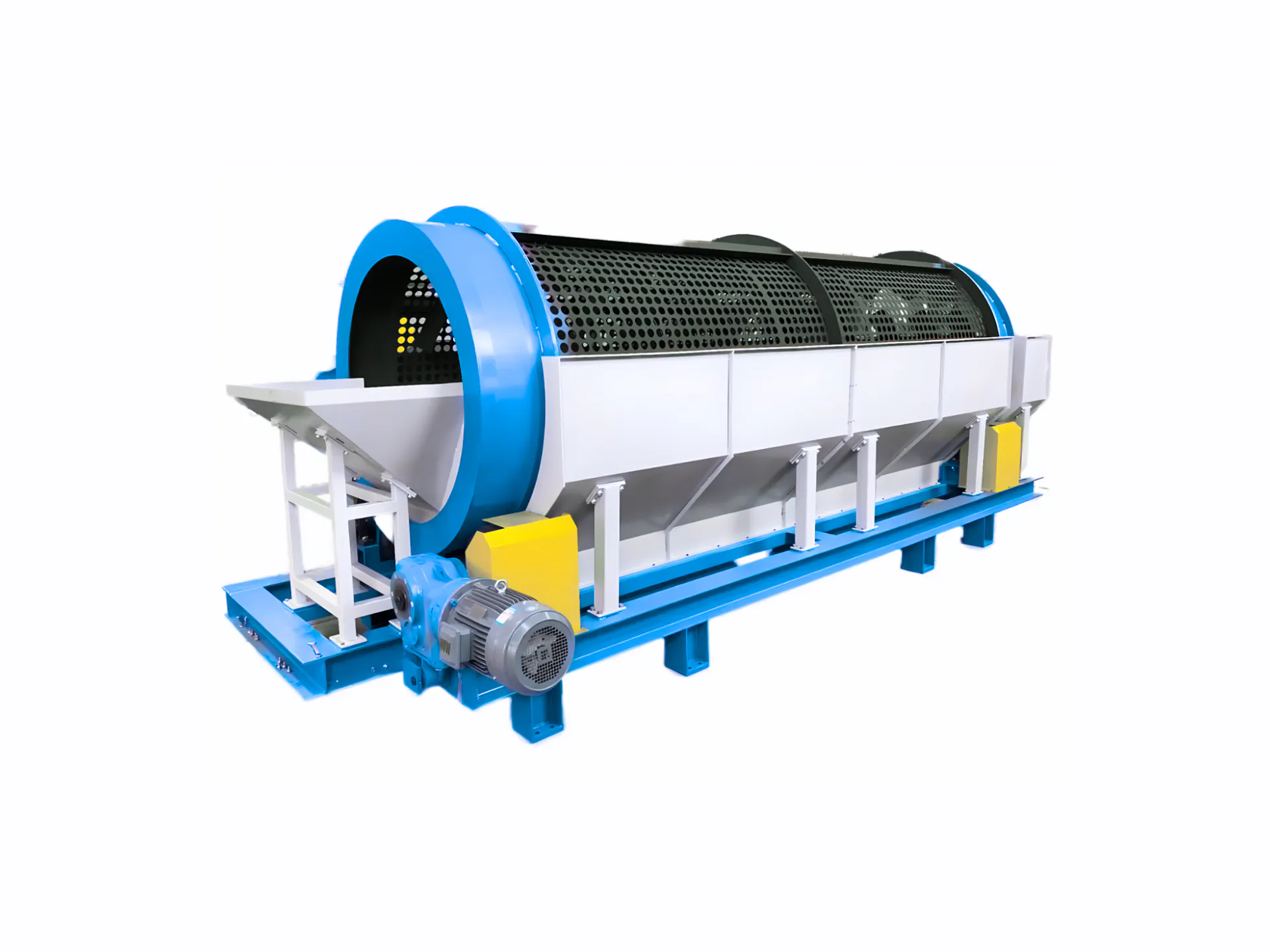

Wet Plastic Crusher/Granulator
Sometimes referred to as a plastic crusher, our plastic granulator machine cuts the PET bottles into small flakes between 10-15mm in size. With water constantly spraying into the cutting chamber, this wet granulation process pre-treats and partially cleans the material before moving onto the next equipment.
Air Classifier
Air classification is a way to separate lighter materials from heavier ones. The main purpose of using the air classifier is to remove contaminations such as paper, cardboard, and plastic labels away from PET flakes.


Sink/Float Separation Tank
Using water as a medium, materials that float are separated from materials that sink. In the case of plastic bottle recycling, PET plastic will sink while plastic film (bottle labels) and PP/PE plastic (bottle caps) will float. A screw conveyor at the bottom of the sink/float separation tank moves the PET plastic to the next piece of equipment.
Hot Washer System
Hot washed PET flakes are of higher value because this process dissolves glues (used to glue labels onto the bottles) and leftover beverages/foods that are difficult to remove in a cold wash process. Although you can just use water in the hot washer system, adding washing agents can be added for better results.

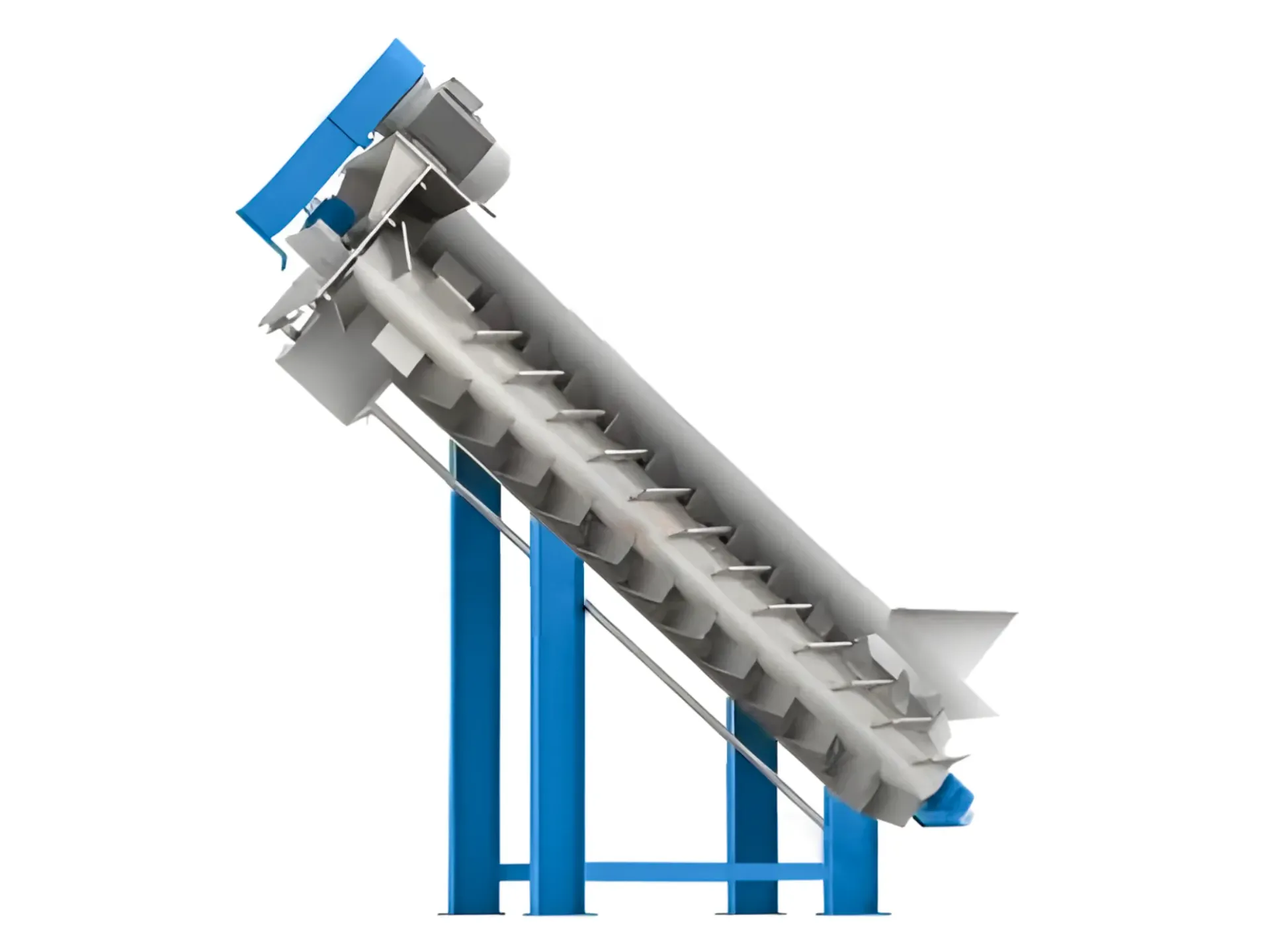
Friction Washer
An efficient piece of cold water washing equipment, the high-speed friction washer uses friction as a mechanical way to remove any hard-to-remove dirt and debris from the PET flakes.
Dewatering Machine
The first step in the drying process, our centrifugal dewatering machine uses centrifugal force to remove a large portion of water within the PET flakes before moving forward onto our thermal dryers.
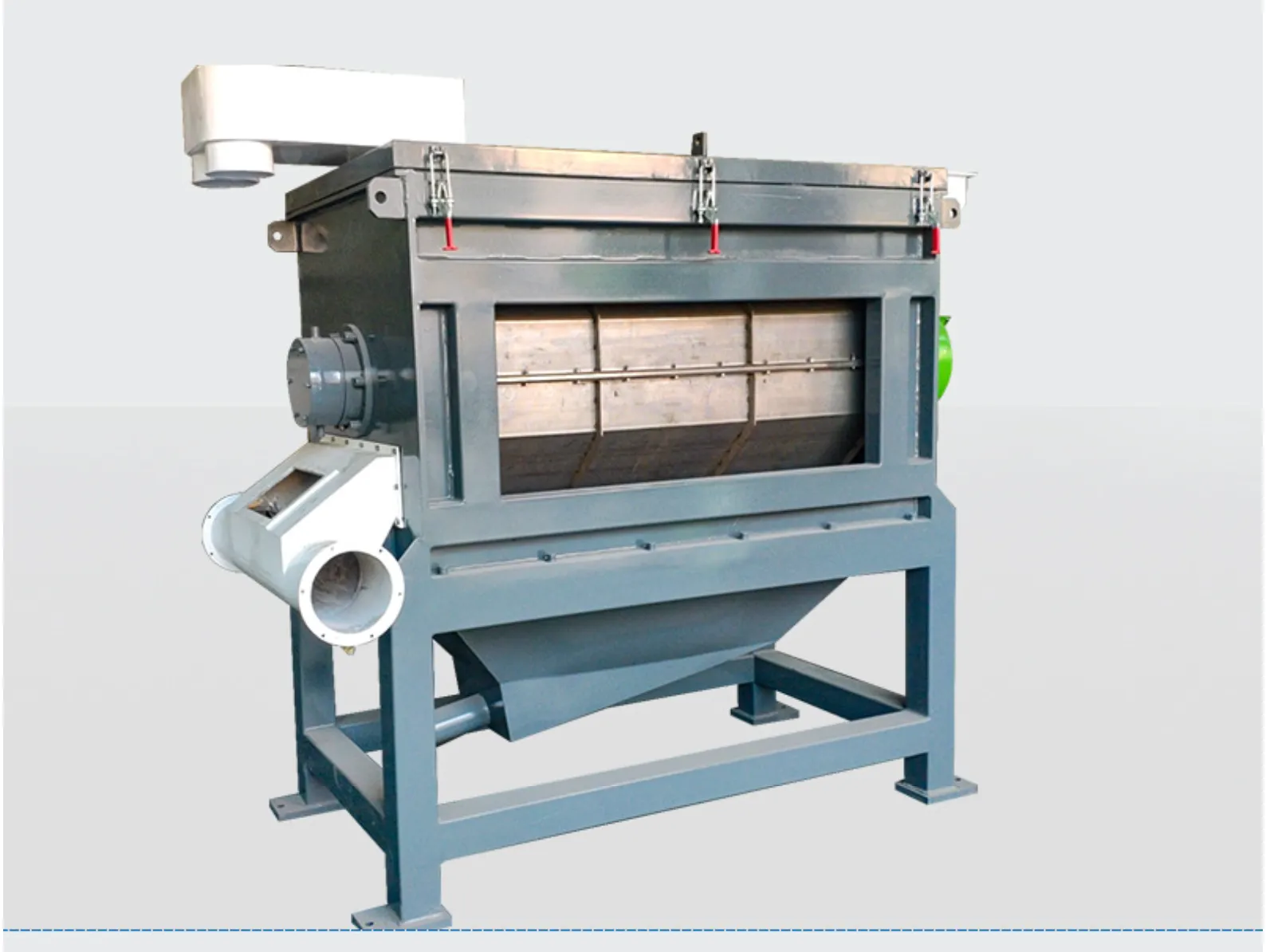
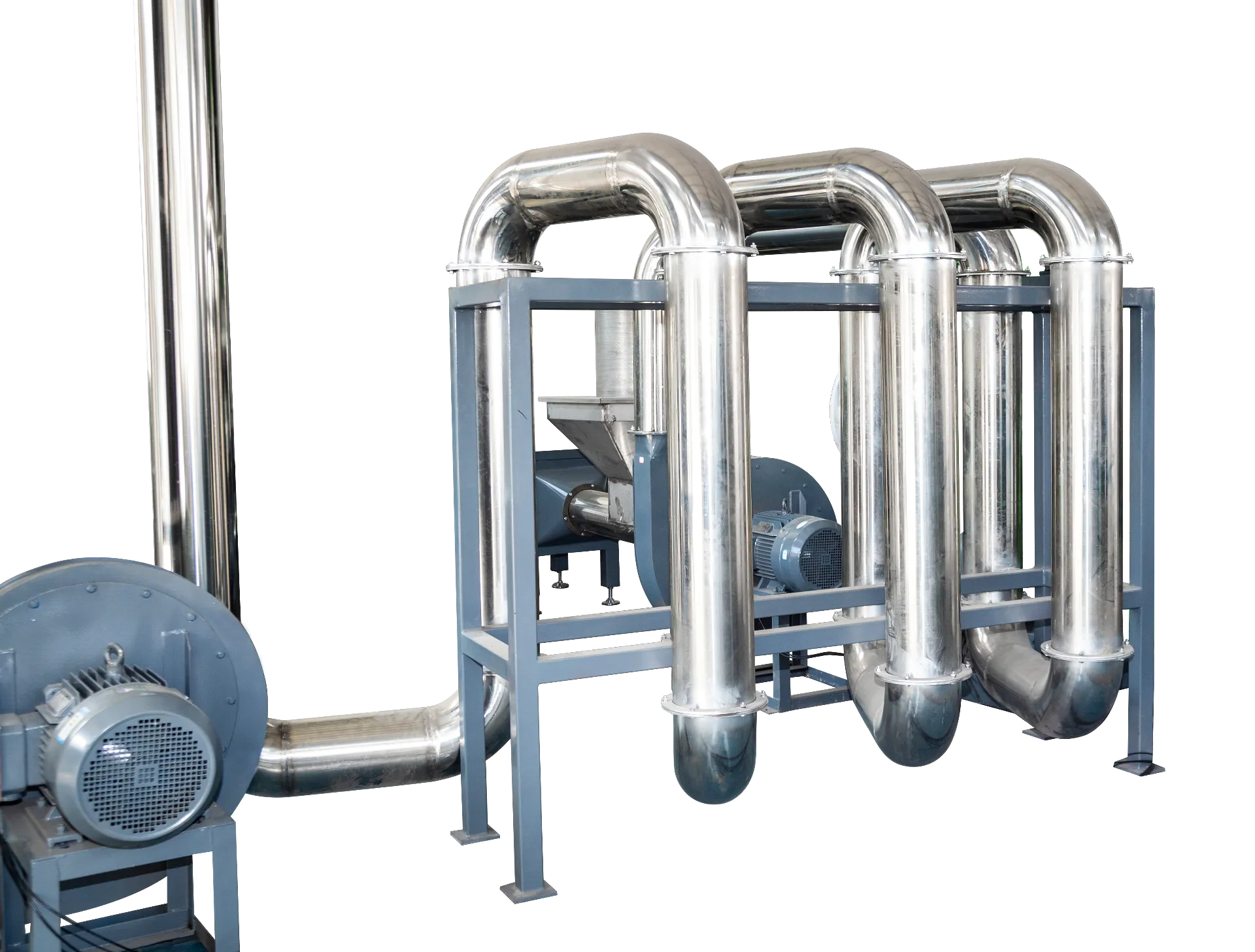
Thermal Dryer
PET flakes are vacuumed out of the dewatering machine into the thermal dryer where they travel down a series of stainless steel tubes mixed with hot air. This process removes any remaining moisture by dehydration. An attached cyclone separator mixes the PET flakes with cool air, preparing them for storage in the product silo.
Product Silo
A storage tank for the clean, dry PET flakes.
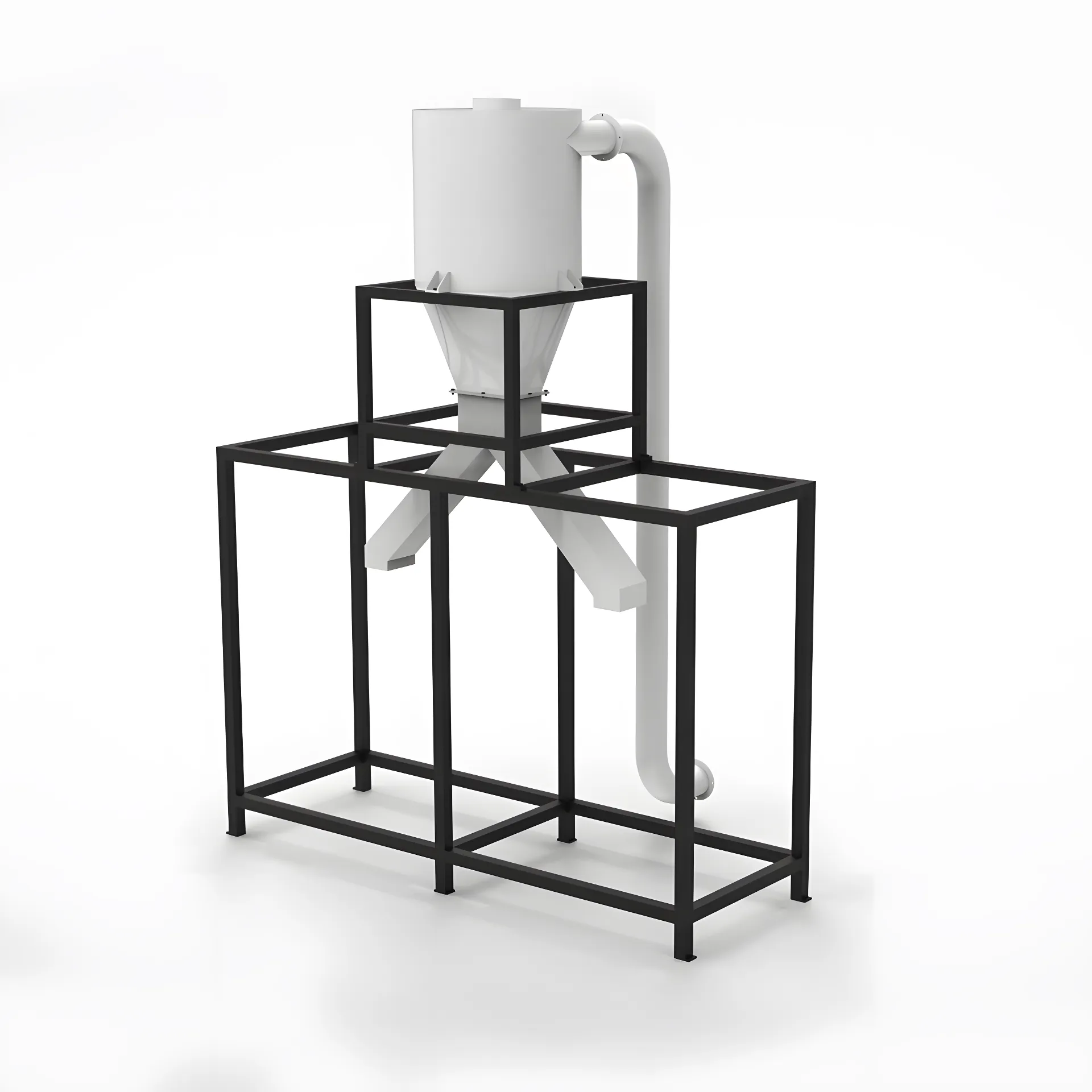

Pelletizer/Extruder
For the most part, PET flakes are used as is, particularly in manufacturing polyester fibers. However, we do have customers requiring plastic pelletizing machines such as our single-screw extruder pelletizers and twin-screw extruder pelletizers.
Flakes Quality Standard Reference Table
Parameter | Standard |
---|---|
Moisture | <0.9% |
PVC | <50ppm |
Glue | <10ppm |
PP/PE | <20ppm |
Metal | <20ppm |
Label | <20ppm |
Color Flake | <30ppm |
PH | Neutral |
Impurity | <100ppm |
Flakes Size | 12mm, 16mm or as per customer requirements |
Plant Parameters
Capacity (kg/h) | Install Power (kw) | Required Area (m²) | Required Staff | Required Steam (kg/h) | Required Compressed Air (Mpa) | Required Water (m³/h) |
---|---|---|---|---|---|---|
500 | 220 | 400 | 8 | 350 | 0.6-0.8 | 1 |
1000 | 500 | 750 | 10 | 500 | 0.6-0.8 | 3 |
2000 | 700 | 1000 | 12 | 800 | 0.6-0.8 | 5 |
3000 | 900 | 1500 | 12 | 1000 | 0.6-0.8 | 6 |
4500 | 1000 | 2200 | 16 | 1300 | 0.6-0.8 | 8 |
6000 | 1200 | 2500 | 16 | 1800 | 0.6-0.8 | 10 |
Frequently Asked Questions
Get the answers to common questions regarding our Recycling Machine
A PET Bottle Recycling Machine is specialized equipment designed to process used polyethylene terephthalate (PET) bottles and convert them into reusable raw materials. This machine typically performs functions like shredding, washing, drying, and pelletizing, effectively preparing the PET for remanufacturing into new products such as fibers, containers, or automotive parts. The efficient operation of a PET recycling machine not only helps in reducing plastic waste but also supports eco-friendly practices by promoting the circular economy.
The operation of a PET Bottle Recycling Machine generally involves several key steps. Firstly, the machine collects and feeds the PET bottles into a shredder, where they are broken down into smaller pieces. Next, these pieces are washed to remove contaminants such as labels, adhesives, and dirt. Following the wash, the clean PET flakes are dried and often pelletized, turning them into small pellets or granules that can be used by manufacturers to create new products. The entire process helps minimize environmental impact and conserves resources.
Utilizing a PET Bottle Recycling Machine provides numerous benefits. Primarily, it contributes significantly to reducing plastic waste in landfills and oceans, combating pollution. Additionally, recycling PET conserves natural resources and energy compared to producing new PET from virgin materials. This machine also fosters economic opportunities by creating jobs in the recycling industry. By converting waste into functional materials, it supports sustainability efforts and encourages responsible consumption, ultimately benefiting the environment and society.
Most PET Bottle Recycling Machines are capable of processing a wide variety of PET bottles, including those used for beverages, household products, and personal care items. It is crucial, however, to ensure that these bottles are adequately cleaned to remove any residual liquids or contaminants. Labels made from paper or plastic can typically be processed; however, heavily adhesive or multilayered packaging might require additional processing techniques. Familiarizing oneself with the machine’s specifications can optimize the recycling process.
The cost of a PET Bottle Recycling Machine can vary significantly based on factors such as size, capacity, automation level, and additional features. Small, basic models may start from a few thousand dollars, while more advanced and larger machines can reach tens or even hundreds of thousands of dollars. Companies must consider their recycling volume and operational requirements when selecting a machine. It’s advisable to perform thorough research and compare options from reputable manufacturers to ensure value for investment.
PET Bottle Recycling Machines can be purchased from Rumtoo Machinery, a specialized manufacturer and supplier focusing on recycling technology. As a provider of industrial machinery, Rumtoo Machinery has a dedicated division for recycling equipment. It’s essential to choose this reputable provider known for quality and customer service. Additionally, exploring online marketplaces and visiting trade shows can offer a wide range of options. Furthermore, contacting local recycling organizations may lead to valuable recommendations and insights into the best machines for your specific needs.
[…] What Are PET Washing Lines? […]
[…] PET bottle washing lines are critical for transforming used plastic bottles into reusable flakes, supporting global recycling efforts. This guide breaks down the process, key components, and considerations for optimizing efficiency and output quality—ideal for businesses investing in sustainable plastic recycling solutions. […]
[…] PET bottle washing lines are critical systems in the recycling industry, designed to transform used polyethylene terephthalate (PET) bottles into clean, reusable PET flakes. These flakes are essential for producing new plastic products, supporting a circular economy, and reducing environmental impact. Given their complexity, maintaining these lines is vital for ensuring efficiency, longevity, and high-quality output. This survey note provides a detailed exploration of maintenance practices, drawing on industry insights and best practices to offer a thorough guide for operators and facility managers. […]
[…] PET bottles undergo a systematic transformation through advanced PET Bottle Washing Line technology, turning waste into high-demand industrial materials. Cleaned PET flakes serve as raw […]
[…] The efficiency of a PET bottle recycling operation depends heavily on the washing and drying process. Advanced centrifugal dryer technologies play a critical role in ensuring high-quality recycled PET (rPET) by removing excess moisture efficiently. For factory managers and investors, selecting the right centrifugal drying system is a strategic decision that impacts operational efficiency, product quality, and long-term cost savings. Below, we explore the key advantages, durability, and value of modern centrifugal dryers in PET washing lines. […]