Our company specializes in providing efficient and sustainable plastic film recycling solutions. We understand the critical need to balance environmental responsibility with the increasing demand for plastic pellets. Our comprehensive plastic film washing line is designed to process polypropylene (PP), polyethylene (PE), and various other types of plastic films. Utilizing cutting-edge technology, our fully automated recycling line integrates a series of machines strategically arranged to maximize efficiency and minimize waste.
In addition to our standard plastic film washing lines, which have capacities ranging from 500kg/h to 3000kg/h, we also offer tailored setups for clients with higher recycling needs. These custom configurations incorporate additional machinery and enhanced capacity, ensuring we meet the specific demands of each client.
Our turnkey solution not only efficiently recycles loose or baled plastic film into high-quality plastic pellets but also plays a vital role in reducing the carbon footprint of plastic waste. By recycling plastic film instead of sending it to landfills, we contribute to a cleaner and healthier environment for future generations.
We take pride in our commitment to sustainability and exceptional customer service. Our team of experts is always ready to assist you in finding the perfect solution for your plastic film recycling needs. Contact us today to discover more about our turnkey solutions and how we can support your recycling goals.
We are pleased to offer you a free solution design service. Our team of experts will design the most suitable plastic film cleaning line solution for you based on your needs and requirements. Please contact us for more information and to start discussing your project.
Working Principle
The entire plastic film washing line is efficiently controlled via a central electric control panel and cabinet. Each piece of equipment is seamlessly connected using conveyors, ensuring a smooth and continuous operation.
Plastic Shredder
To prevent long pieces of plastic film from tangling (imagine saran wrap) and clogging conveyors and rotary-based machines, the first step involves cutting the plastic film into smaller, manageable pieces using a plastic shredder machine. The resulting plastic pieces are typically around 1-5 inches in size.
Plastic Granulator
The plastic granulator further reduces the plastic film into even smaller pieces, approximately 10-20mm in size. With water constantly injected into the cutting chamber, our wet granulation process not only cuts but also pre-treats and partially cleans the plastic film before it moves onto the next machine.
Friction Washer
Our high-power cold water friction washer spins at nearly 1,000 rotations per minute. As the PP/PE films enter the friction washer, the plastic film rubs against each other at high speeds, effectively removing hard-to-remove contamination. Simultaneously, any paper and cardboard are broken down into fibers and removed. While one friction washer is standard, various washing plants have requested a secondary friction washer to ensure thorough cleanliness.
Sink Float Separation Tank
Utilizing water as a medium, materials that float are separated from those that sink. In plastic film recycling, PP and PE films will float, while heavier contaminants such as dirt, sand, glass, metals, and other plastics will sink. A screw conveyor at the bottom of the sink float separation tank removes these contaminants. Beyond separation, this apparatus also further cleans the plastic film.
Centrifugal Dewatering Machine
The first step in the drying process, our centrifugal dewatering machine uses centrifugal force to remove a significant portion of water from the plastic film before it moves onto the thermal dryers. Since thermal dryers use heat to dehydrate water, they consume more energy. Therefore, the dewatering machine is beneficial for long-term operational cost savings.
Screw Press Dewatering Machine
An optional piece of equipment, the screw-press dewatering machine is a more advanced version of the standard dewatering machine. Instead of using centrifugal force, the screw press squeezes water out via high pressure. This machine can replace both the dewatering machine and thermal dryers.
Thermal Dryer + Cyclone Separator
The clean plastic film is vacuumed out of the dewatering machine and into the thermal dryer system, where it travels down a series of stainless steel tubes mixed with hot air. The remaining moisture is dehydrated in this process, which concludes with a cyclone separator. The cyclone separator allows the plastic film to mix with a fresh stream of cold air, preparing it for storage in the product silo. It also effectively removes fines and dust.
Product Silo
A storage tank for the clean, dry pieces of plastic film.
Plastic Pelletizing Machine
The final and perhaps most crucial step in plastic film recycling involves processing the clean film into plastic pellets before it can be used in production. To achieve this, we offer a specialized plastic film water ring pelletizer system that produces high-quality, round plastic pellets.
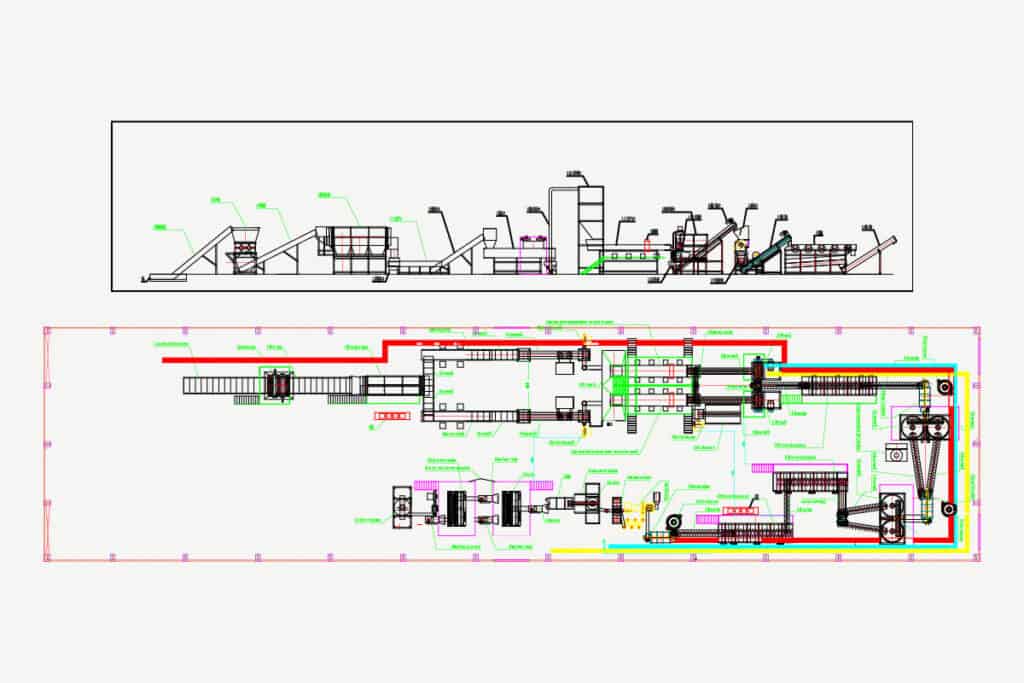
Warranty
All recycling machines come with a 1 year limited warranty.
INQUIRIES
To get the latest prices and lead times, send us a message using the form below.